AI is now driving smarter decisions on the factory floor, from AI agents that assist machine operators in real-time, to powerful models of predictive maintenance that anticipate supply chain disruptions.
With a growing list of use cases of AI in Manufacturing, how factories think, adapt, and operate is reshaped. Therefore, understanding these applications is key to staying competitive in today’s industrial landscape.
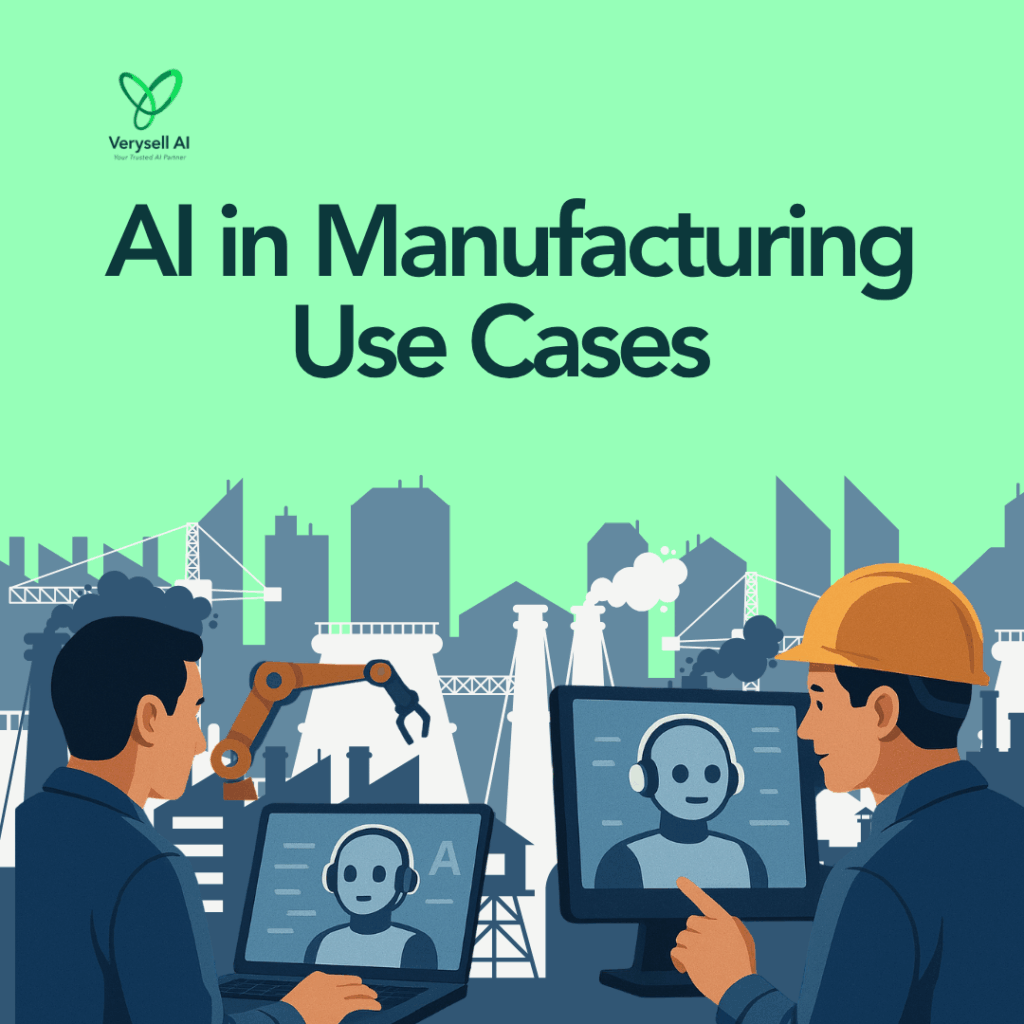
1. How AI is Reshaping Manufacturing
AI is no longer just an automation tool. It’s an advisor, a forecaster, and a decision-maker. Modern AI systems can process machine data in real time, interpret natural language questions, simulate supply chain scenarios, and analyse customer feedback to guide product development.
What makes AI especially powerful in manufacturing is its ability to:
- Learn from patterns in historical and real-time data
- Interact with humans through natural language interfaces
- Integrate seamlessly with enterprise systems Enterprise Resource Planning (ERP), Manufacturing Execution System (MES), and Product Lifecycle Management (PLM)
- Generate contextual recommendations instantly
The result? Higher productivity, safer operations, smarter decisions, and a competitive edge in today’s volatile market.
2. Top AI Use Cases in Manufacturing
Here’s a breakdown of the top AI in manufacturing use cases that are actively reshaping factory floors.
2.1. AI Copilot for Machine Operators
Machine operators, especially new hires, often lack the experience to manage complex machinery, leading industry executives to estimate unplanned downtime costs at around $50 billion per year with human error being a primary factor. Siemens found that downtime drains 11% of revenue for the world’s largest manufacturers, about $1.4 trillion annually, and automotive plants can lose up to 3 million per hour during stoppages.
AI can act as a real-time assistant for machine operators by interpreting machine status data and delivering instant, natural language recommendations. The AI integrates machine knowledge and presents contextual visualizations to guide operator decisions, leading to increased efficiency, faster training, and reduced risk of errors or accidents.
Key Features:
- Natural language interaction
- Contextual data visualization
- Machine knowledge integration
Potential outcomes:
- Significant reduction in quality control process errors and downtime
- Improved safety and compliance
- Accelerated training through interactive assistance, resulting in faster onboarding
- Higher machine uptime
2.2. AI-powered Factory Agent
In modern manufacturing, manufacturers face three major challenges when it comes to production data: delayed access, time-consuming manual processes, and fragmented data systems. A 2023 SME–Laserfiche study found that 62% of manufacturers experience operational delays due to slow access to inventory and production data. On average, employees spend up to 30% of their time just searching for information across siloed systems. Meanwhile, factories that still rely on manual machine data collection risk reporting lags of days or weeks, limiting timely decision-making.
The AI-powered Factory Agent addresses all these challenges by process automation. It enables users, whether line managers or C-level executives, to simply ask, “What’s today’s production output?” or “Do we have enough inventory for next week’s batch?”. The AI queries relevant databases instantly and returns clean, contextualized answers through dashboards or visual summaries. It support natural language processing, integrated analytics, and live data feeds, turning complex reporting processes into a matter of seconds.
Key Features:
- Natural language dashboard queries
- Real-time visualization
- Unified data access
Potential outcomes:
- Quicker and more informed decision-making across management levels.
- Streamlined data access, improving operational response time.
- Enhanced productivity and performance tracking.
2.3. Customer Feedback Agent
Manufacturers today receive enormous volumes of customer feedback across channels like surveys, support tickets, and social media. However, most of it remains underutilized. This leads to delayed issue resolution, missed insights on product performance, and slower innovation cycles. Without a systematic approach to feedback analysis, companies risk overlooking recurring problems and damaging customer trust.
An AI-powered feedback agent can dramatically change how businesses handle customer sentiment and service. By using natural language processing and sentiment analysis, it can summarize complaints, categorize trends, and cluster recurring issues for product teams to act on. It can also automatically generate or suggest responses to common inquiries, enhancing both speed and quality in customer support.
Key Features:
- Sentiment analysis of customer messages across multiple platforms
- Categorization and clustering of feedback by product or issue
- Auto-summarization of key themes for reporting and decision-making
- AI-generated response suggestions for common support queries
Potential outcomes:
- Faster response times and improved customer satisfaction
- Early identification of product defects or service gaps
- Actionable insights to support product improvement
- Strengthened brand loyalty through timely customer interaction
2.4. AI-Powered Procurement Agent
Procurement is a critical yet time-consuming function, often leading to delays in production due to contract backlogs, supplier vetting, and inefficient purchasing processes. The Deloitte Global CPO Survey reveals that 89% of procurement teams experience increased errors and inefficiencies due to manual vendor management processes. These inaccuracies often result in incorrect purchase orders, mismatched payments, and potential legal complications. Over time, such errors can significantly impact both a company’s finances and its reputation.
AI-powered procurement agents can assist procurement teams with intelligent automation and decision support. It can read contracts, highlight compliance risks, compare supplier performance, and prompt or automate purchase orders via natural language. The result? Quicker cycle times, reduced administrative burden, and smarter vendor selection.
Key Features:
- Contract review automation to scan and highlight missing clauses, or non-compliance rates between contracts and invoices, and detect duplicate invoices
- Vendor research and ranking based on past performance, certifications, pricing, and delivery timelines
- Automated purchase order processing (autofill, check and send purchase orders) to ensue alignment with procurement policies
- Global procurement management, navigating regional compliance and currency exchange to recommend best-fit international vendors
Potential outcomes:
- Shorter procurement cycles
- Reduced manual work, less errors and fraud
- Better compliance and lower risk with contract AI audits
- Optimized sourcing across regions
2.5. AI for Supply Chain Risk Analysis
Global supply chains are more fragile than ever. QIMA’s 2025 Global Sourcing Survey found that just 13% of businesses have full visibility into their sourcing networks, while 54% can only identify over half their suppliers.
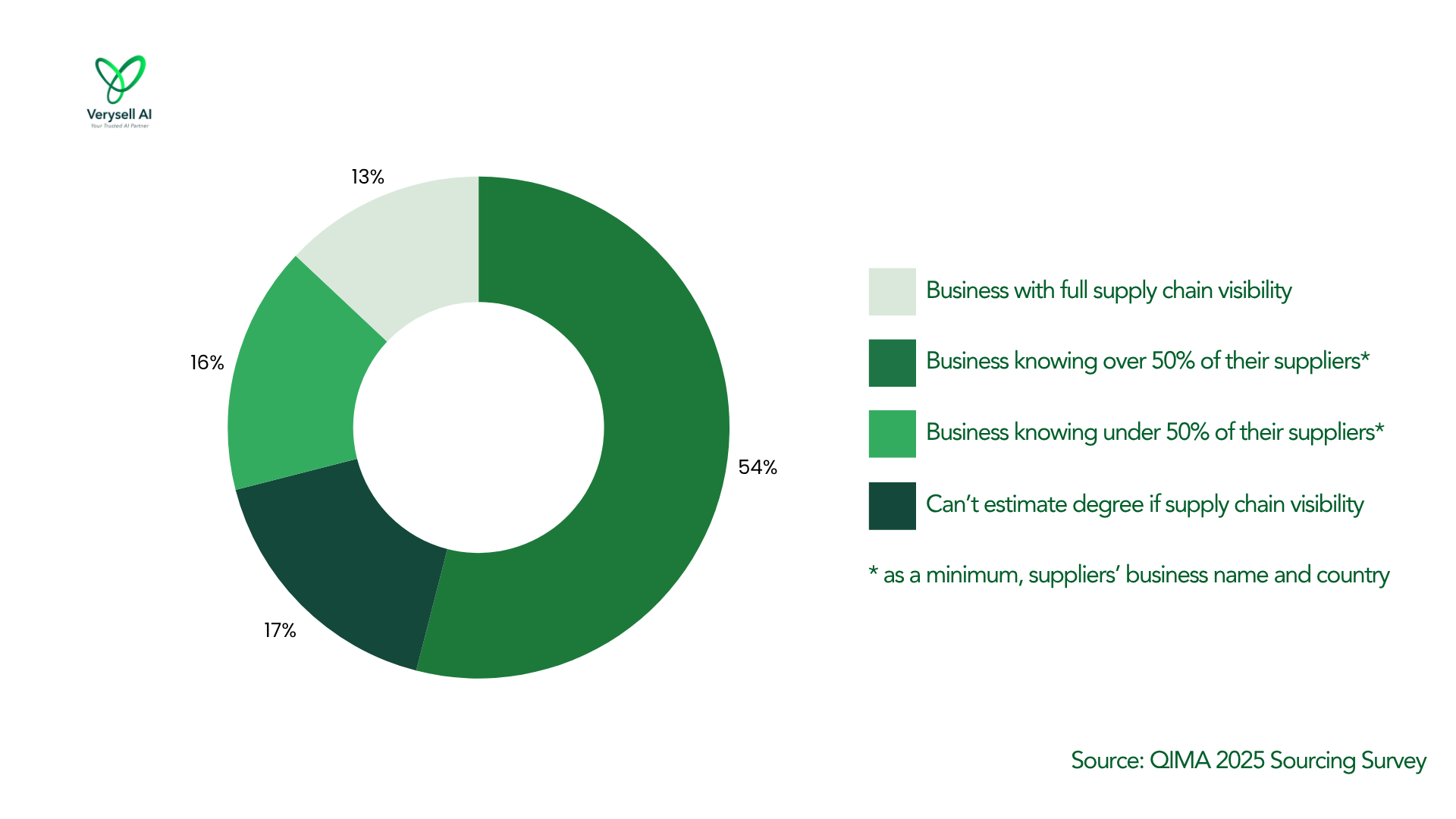
Without comprehensive tracking, companies struggle to anticipate disruptions such as geopolitical shifts, material shortages, or transportation delays. Each disruption can inflict serious financial damage. Large manufacturers often lose millions per day when production stalls.
An AI-powered risk agent consolidates internal (contracts, pricing, supplier performance) and external (news, geopolitics, logistics) data, simulates disruption scenarios, highlights vulnerable suppliers, and recommends contingency plans.
Key Features:
- Real-time scanning of geopolitical and logistics risk factors
- Scenario modeling (e.g., port closures, cost spikes)
- Supplier performance profiling and compliance evaluation
- AI-enabled contract reviews to flag risky clauses
- Price and inventory trend forecasting
Potential Outcomes:
- Early identification of supply chain threats –> Faster risk response
- Better sourcing decisions
- Informed rerouting or dual-sourcing decisions
- Better cost control and inventory planning
- Reduced impact from unforeseen disruptions
2.6. Predictive Maintenance
According to Global Trade (2024), though predictive maintenance is proven to cut unplanned downtime by 30 – 50% and extend equipment life by 20 – 40%, only 41% of manufacturers have adopted it; the rest remain reactive. This limits responsiveness and inflates costs. Reactive maintenance now commands up to 80% of technician time and unplanned machine breakdowns lead to costly maintenance costs and repairs, as well as prolonged downtime.
The AI predictive maintenance agent addresses these issues by analyzing real-time sensor data, predicting failures, and delivering actionable instructions: text, images, or videos… in multiple languages. It also automates service scheduling and generates compliance-ready reports.
Key Features:
- Live monitoring of operational data (vibration, temperature, etc.), giving analysis of performance data to detect early signs of wear and tear, decline in efficiency, or possible failures.
- Automated alerts sent to the maintenance team when potential issues are detected.
- Multiformat guidance based on predicted issues
- Support for multilingual teams and global documentation
- Dashboard for real-time performance tracking and maintenance scheduling.
Potential Outcomes:
- Reduced unplanned downtime and repair delays
- Improved utilization of technicians and parts
- Lower maintenance costs.
- Consistent maintenance across multilingual, multi-site teams
3. Benefits of AI in Manufacturing
AI adoption delivers clear and cross-functional advantages in modern manufacturing:
- Reduced downtime & maintenance costs: As shown in the predictive maintenance use case, AI enables real-time monitoring of equipment and early detection of mechanical issues. This reduces unplanned downtime, one of the most costly issues in manufacturing, by up to 50% and increase machine life up to 40% (Global Trade, 2024). For example, McKinsey estimates that AI-driven predictive maintenance can reduce maintenance costs by up to 25%, and improve overall equipment effectiveness (OEE) by 20% (McKinsey & Company, 2021). Maintenance teams can act on AI-generated alerts, follow multilingual, multimedia repair guides, and better allocate resources, resulting in fewer interruptions and more predictable operations.
- Faster, smarter decisions: Instead of spending 30% of their time searching for information (RDA Accountants), operators and managers can query dashboards using natural language and get real-time answers. This accelerates daily operations, enhances production planning, and improves responsiveness to supply or inventory changes.
- Higher Procurement Accuracy & Efficiency: Organizations using AI-driven procurement report 40% reductions in overall procurement costs within just six months, thanks to predictive analytics and automated sourcing workflows. One case study showed a global firm saving over 10,000 hours per year in manual tasks after deploying RPA-powered pricing updates and forecasting tools (Hudson&Hayes, 2024). Moreover, manufacturing-specific research highlights 28% faster component sourcing and a 23% reduction in material costs thanks to AI-powered procurement systems. These results illustrate that intelligent procurement automates error-prone tasks, accelerates sourcing decisions, and delivers rapid, measurable improvements in both accuracy and efficiency.
4. Challenges of AI Adoption in Manufacturing
Despite its benefits, AI integration in manufacturing presents several hurdles:
- Integrating Fragmented Data Systems: AI relies on real-time inputs from ERP, MES… and machine sensors. However, many factories still use siloed systems or paper logs. Ensuring clean, consistent, and integrated data is a major but necessary undertaking.
- Workforce adaptation: AI tools don’t offer benefits unless used effectively. Shop-floor staff and managers need intuitive interfaces and hands-on training. Without this, even the most advanced AI systems—like factory dashboards or procurement bots—can be underutilized or ignored.
- Upfront investment: Building AI platforms with domain-specific integrations and real-time data pipelines requires significant initial investment. However, starting with a focused PoC and clearly measurable use cases (like predictive maintenance or procurement automation) helps validate ROI and build momentum for broader deployment.
- Cybersecurity concerns: As factories digitize operations, the attack surface increases, requiring stronger data governance and system security.
5. How to Get Started?
Due to aforementioned challenges, AI in manufacturing requires a thoughtful, phased approach, starting with tangible problems and scaling based on results. Here’s a step-by-step guide to make the transition smooth and effective:
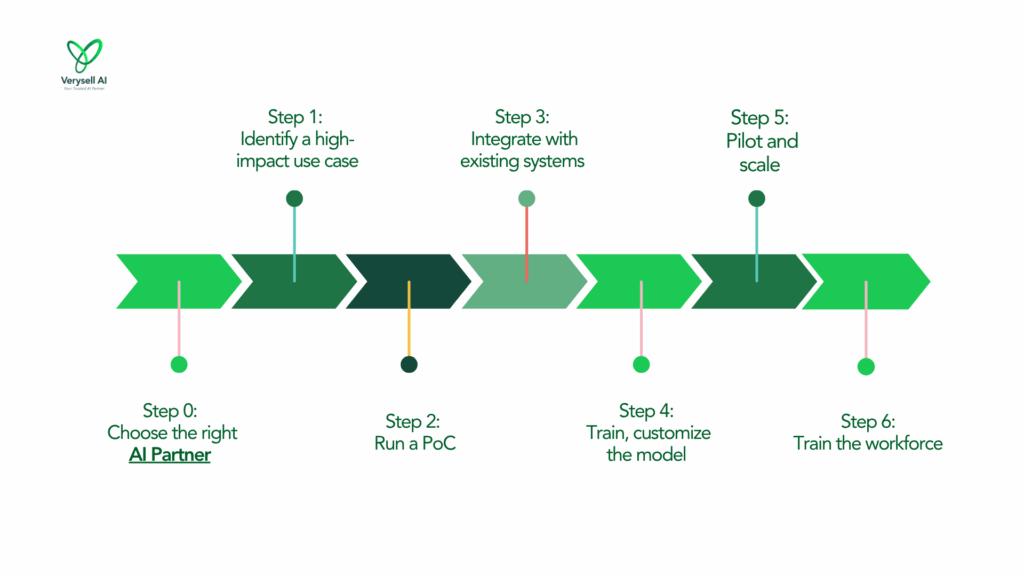
Step 1: Identify a High-Impact Use Case
Begin with a use case that directly addresses pressing pain points and has measurable ROI potential. Typical entry points include:
- Predictive maintenance to minimize unplanned downtime
- Real-time factory dashboarding for faster decisions
- Procurement automation to eliminate inefficiencies
Step 2: Run a Proof of Concept (PoC)
Start small. Test the solution on one production line or department using a limited dataset (historical + live) to validate feasibility and assess ROI. This helps build internal confidence and uncover integration needs early.
Step 3: Integrate with Existing Systems
Connect AI to your digital ecosystem: real-time machine data, ERP, MES, CRM, or customer feedback platforms. Seamless integration is key to unlocking insights and automation.
Step 4: Train and Customize the Model
Refine the AI with historical data and domain-specific logic. Ensure data quality and availability by digitizing key records and aligning with standards in systems like MES, ERP, or SCADA.
Step 5: Pilot and Scale
Deploy the AI solution in a limited operational setting. Gather feedback, measure business impact, and iteratively enhance the system before scaling to other lines or factories.
Step 6: Train the Workforce
Equip operators, engineers, and managers with hands-on training and documentation. Adoption only succeeds when the workforce is confident using the new tools.
(Step 0): Choose the Right AI Partner
While these steps build the foundation, success ultimately hinges on choosing the right partner. A provider like Verysell AI brings deep manufacturing experience and a modular integration approach. Our custom AI & ML or 10-week Product-Ready Program are ideal to assist businesses solve unique challenges, understanding each company’s demands and tailoring AI solution to meet those.
What’s next?
AI isn’t just another buzzword in manufacturing. It’s a practical tool driving real-world outcomes. From helping operators ask, “What do I do now?” to forecasting supply chain disruptions before they hit, AI is the co-pilot every smart factory needs.
At Verysell AI, we specialize in helping manufacturers unlock the full potential of AI through our proven, modular solutions and hands-on support. Whether you’re aiming to reduce downtime with predictive maintenance or streamline procurement with intelligent automation, our AI/ML Engineers & Consultants will guide you from concept to deployment with speed and confidence.
Ready to elevate your manufacturing operations? Contact us today and start your AI transformation journey with a partner who understands your challenges and delivers real impact.