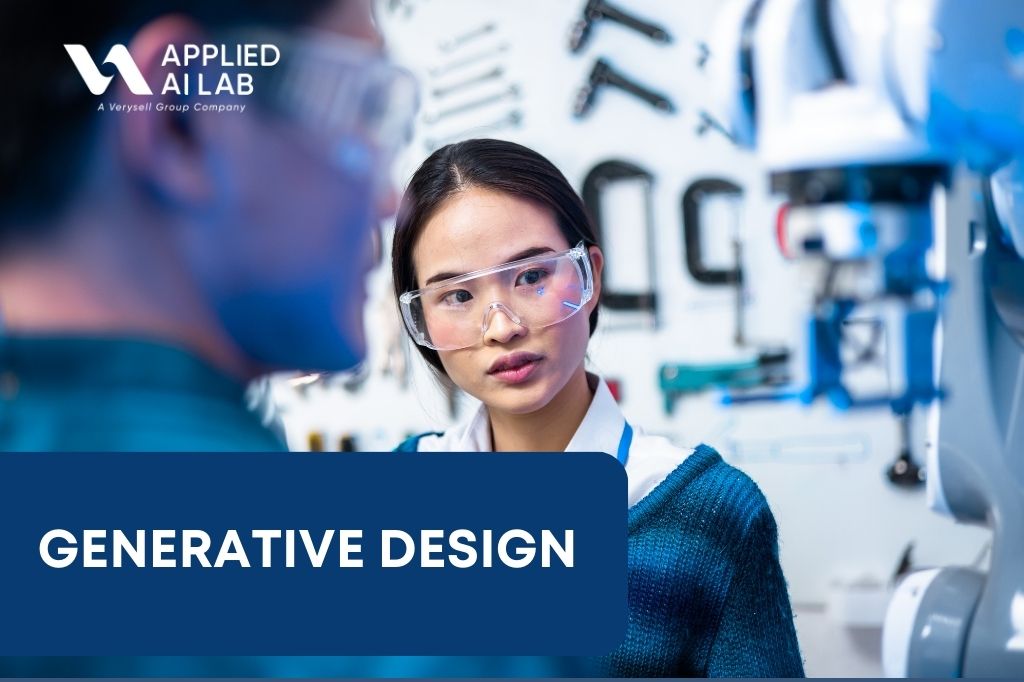
Business Challenges
For manufacturing businesses, the design phase has long been a bottleneck characterized by labor-intensive processes, limited innovation, and slow time-to-market. Human-led design initiatives often face constraints in terms of exploring multiple design possibilities efficiently, due to the limitations of manual calculations and traditional Computer-Aided Design (CAD) systems. Consequently, this traditional approach not only stifles innovation but also prolongs the product development lifecycle.
Traditionally, experts have led the design process, relying heavily on their experience and CAD systems to develop and refine product designs. However, this method has its downsides. It can be time-consuming, costly, and restricted in its capacity to consider an extensive range of design permutations. The traditional processes often result in suboptimal designs that may be neither cost-effective nor sustainable.
By utilizing Generative AI, the design process is significantly improved, capable of exploring a multitude of design combinations that were previously unfeasible. The technology adheres to various parameters and constraints in the design domain, optimizing both efficiency and performance. Furthermore, AI Vision allows manufacturers to visualize and iterate designs at an unprecedented pace, leading to faster, more innovative, cost-effective, and sustainable manufacturing practices.
AI Solution
To tap into the potential of generative design, a solution focusing on part design, such as car wheels, was developed. Car wheel design goes beyond aesthetics, encompassing crucial dynamical properties like force ratios (normal/shear), volume ratios, and CAE (Computer-Aided Engineering) analysis. Here’s how the solution was crafted:
- Generative Adversarial Neural Networks (GAN): A GAN model was employed to generate diverse 2D models of car wheels, introducing variability in outer shapes and appearances.
- 3D Reconstruction: The 2D models were then fed into 3D modeling modules of Computer-Aided Design (CAD) software to reconstruct their corresponding 3D models of car wheels.
- CAE Analysis: CAE analysis, vital for validating the dynamical properties of the designs, was conducted using CAD/CAE software.
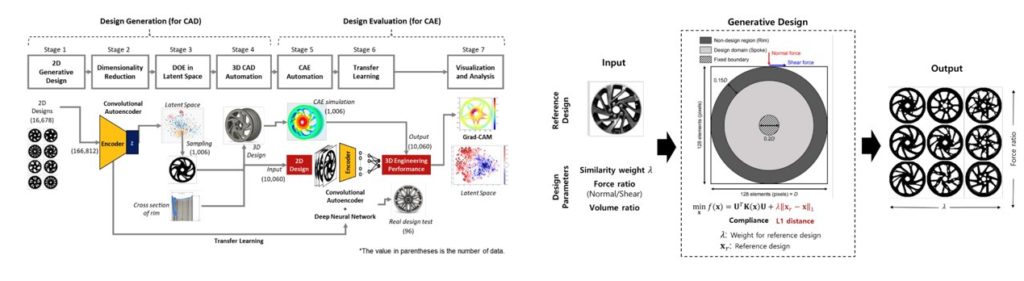
Expected Outcome
The end-to-end solution brings forth a host of benefits, including:
- Reduced Dependency on Skilled Engineers: By automating the car wheel design process, the solution alleviates the burden associated with a shortage of skilled engineers, making the design process more accessible.
- Accelerated Time to Market: The automation of design processes reduces the time required to bring car wheels to market, enhancing competitiveness.
- Exploration of Novel Designs: Through the generative design approach, the solution opens avenues for discovering new and visually appealing car wheel designs, broadening the design landscape.
In summary, the integration of generative design powered by Generative AI revolutionizes the design process, particularly in the realm of car wheels. By automating and expanding design possibilities, this solution not only streamlines operations but also fosters innovation in product design and development.